Important Considerations Regarding the Continued Use of Old Refinery Equipment
February 9, 2021
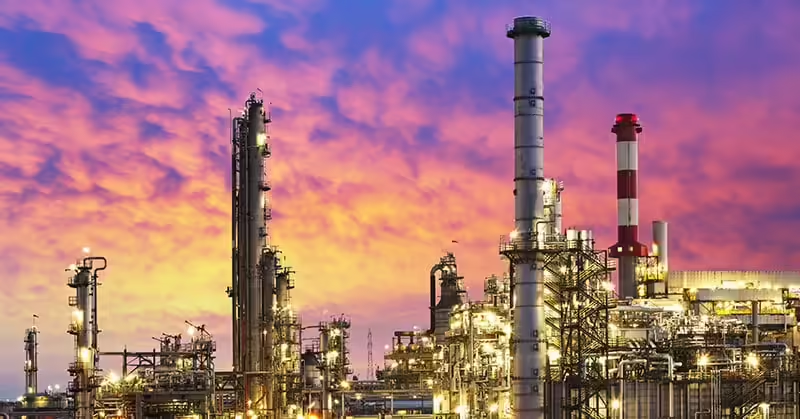
Since the late 1800’s, the United States has emerged as a leader with respect to industrial work. Much of the United States’ development began along the eastern coast and worked its way west. Texas (and especially the cities located near the Gulf of Mexico) became very industrialized during this time period. With the expansion of the railroad and offshore shipping channels, multiple cities close to the Gulf of Mexico—Houston, Beaumont, Port Arthur, Galveston, and Corpus Christi—were able to establish refineries and chemical plants which still operate to this day. As of January 1, 2020, four of the top ten largest oil refineries in the United States are presently located along the Texas coast. Here are the top 3 refineries in Texas:
Rank | Oil Refineries | Location | Barrels per day |
---|---|---|---|
#1 | Motiva Enterprises, LLC | Port Arthur, TX | 607,000 |
#2 | Marathon Petroleum Co. LP. | Galveston, TX | 585,000 |
#3 | ExxonMobil Refining and Supply Co. | Baytown, TX | 560,500 |
Despite the benefits that are associated with the industrial development in Texas, many risks of catastrophic events continue to remain due to the continued use of old equipment that has now become defective. Countless industrial workers continue to suffer tragic injuries—including amputation, traumatic brain injury, or death—while employed by these industrial companies. According to the Bureau of Labor Statistics (BLS), private industry employers reported 2.8 million nonfatal workplace injuries and illnesses in 2019. These statistics, coupled with industrial plants that continue to use old equipment which arguably may be defective, require the consideration of important questions:
What Are My Employer’s Duties Regarding Worker Safety Involving Old Refinery Equipment that May Be Defective?
All employers have a duty to provide a safe workplace for refinery workers. Part of this duty requires the routine inspection of all equipment. According to the Occupation of Safety and Health Administration (“OSHA”), an employer is required to comply with the following to ensure the integrity of the machinery and machine safeguards:
- Manufacturer’s recommendations;
- Good engineering practice; and
- Any applicable OSHA provisions (such as the mechanical power press inspection and maintenance requirements, contained in 1910.217(e).
Manufacturer’s Recommendations
Following a manufacturer’s recommendations can help save companies money from not having to replace equipment that is capable of staying in use for longer periods of time, but more importantly, it helps keep workers safe. Preventive maintenance is a fundamental procedure that should be performed on a routine basis—sometimes as often as the beginning and end of each shift. Examples of preventive maintenance on equipment and other machinery found in refineries are:
- Ensuring that machines are clean of debris (e.g. shavings, scale, or grease)
- Ensuring that tools are sharpened (e.g. knives, saw blades or box cutters)
- Replacing worn or damaged tools
- Inspecting fluid-driven equipment for leaks and/or properly maintain fluid levels
- Inspecting belts, slings, and straps that have frayed or begun to tear
- Inspecting tongs for signs of warping
When old equipment is discovered to be defective or dangerous, it should be removed immediately to keep workers safe.
Good Engineering Practice
On May 11, 2016, OSHA released a memorandum discussing “good engineering practices.” Three provisions to good engineering practices are:
- Employers that document that all equipment in Process Safety Management-covered processes comply with OSHA recognized and generally accepted good engineering practices (RAGAGEP)
- Inspections and tests are performed on process equipment subject to the standard’s mechanical integrity requirements in accordance with RAGAGEP
- Inspection and test frequency follows manufacturer’s recommendations and good engineering practice, and more frequently if indicated by operating experience
Employers dedicated to maintaining good engineering practice within the workplace promote worker safety and prevent catastrophic injuries from occurring.
Other Applicable OSHA Provisions
All employers are required to implement and follow safe practices within the workplace. Many of these safe practices can be found on OSHA’s website. Some examples of OSHA requirements for industrial employers are:
- 217(b) – mechanical power press guarding and construction
- 217(b)(1) – hazards to personnel associated with broken or falling machine components. Machine components shall be designed, secured, or covered to minimize hazards caused by breakage, or loosening and falling or release of mechanical energy (i.e. broken springs)
- 217(b)(8)(i) – a main power disconnect switch capable of being locked only in the Off position shall be provided with every power press control system
- 217(b)(8)(ii) – the motor start button shall be protected against accidental operation
- 217(c)(3)(iii)(f) – guards shall be used to protect all areas of entry to the point of operation not protected by the presence sensing device
What is the Time Period in Which I Can Bring a Product Liability Claim in Texas?
A person wishing to sue under a product liability claim should be aware of certain time constraints that apply under the Civil Practices & Remedies Code (“CPRC”). CPRC 16.012(b) states that “except as provided by subsections (c), (d), and (d-1), a claimant must commence a product liability action against a manufacturer or seller of a product before the end of 15 years after the date of the sale of the product by the defendant.”
The significance of the statute of repose is that under CPRC 16.012(b), the time to sue a product manufacturer could have already passed before anybody was injured by the product, or be very close to the time of injury. Here is a hypothetical where John Doe seeks to bring a product liability claim against ABC corporation based on a claim that the heavy machinery he was using was defective:
- ABC corporation manufactures a piece of heavy machinery on March 1, 2006
- John Doe is injured while using the heavy machinery on January 1, 2021
- Assuming none of the exceptions under CPRC 16.012 apply, John Doe’s deadline to commence a product liability action in Texas is March 1, 2021
What Kind of Damages Can I Seek If I Was Injured By Defective Refinery Equipment?
Injuries caused by defective equipment are generally recoverable under strict liability in tort. When you hire us to represent you, we will help you seek compensation for:
- Medical expenses
- Lost income and earning capacity
- Scarring and disfigurement
- Pain and suffering
- Emotional distress
- Loss of enjoyment of life and impairments to your family relationships
- Punitive damages
- Other physical, financial, and emotional harm
What Should I Do If I Was Injured By A Defective Refinery Equipment?
If you or a loved one has been seriously injured or tragically killed at a refinery by defective equipment, you have legal rights that should be handled by experienced refinery accident attorneys. Call Morrow & Sheppard LLP today at 800-489-2216 for a free, confidential consultation regarding your refinery accident and injuries.
- Home
- |
- Plant, Refinery & Industrial Accidents
- |
- Important Considerations Regarding the Continued...